帶輪作為一種重要的傳動零件, 廣泛應用于汽車、農機、水泵以及機床等機械設備傳動中。帶輪傳統加工方法是采用鑄、鍛毛坯經切削加工而成,特點是浪費材料、生產效率低,產品具有精度低、笨重、轉動慣量大等缺點。隨著科學技術的發展進步,鍛壓及旋壓技術以其節能節材、生產效率高、產品性能好、合格率高等優點,逐步推廣應用到帶輪的實際生產中。
帶有凸臺的多楔帶輪的成形采取鍛壓與旋壓相結合的成形工藝,而關于影響復雜結構多楔帶輪成形質量的工藝參數,并沒有明確的研究結果可以參考,故零件生產多結合有限元模擬和試驗分析得到較為合適的參數,并在此基礎上進行下一步的優化。根據材料的拉伸系數計算拉伸道次,結合沖壓與鍛造技術并采用有限元模擬軟件DEFORM-3D進行數值模擬,分析成形過程中的應力、應變分布,為鍛壓成形多楔帶輪的實際生產提供參考。
零件結構分析
帶有凸臺的多楔帶輪結構如圖1、圖2所示,在旋壓成形多楔齒之前需經過鍛壓成形內筒及凸臺,其中凸臺的成形難度較大。多楔帶輪材料為DD13鋼,基本力學性能如下:屈服強度為325MPa,密度為7.851g/cm3,彈性模量為205GPa,泊松比為0.29。
鍛壓成形工藝分析
根據體積不變原理,利用Pro/Engineer對多楔帶輪體積進行計算,同時考慮預留加工余量,確定選用厚度為3mm,直徑為206mm的板坯進行制坯。根據零件結構特點制定其鍛壓成形工藝路線:多道次拉深成形內筒→冷鍛內筒→成形凸臺→成形外圓弧。
內筒的多道次拉深成形工藝參數可查詢沖壓手冊,為盡可能降低板坯減薄程度,設計三道次拉深成形內筒。通過查閱帶凸緣拉深系數表并且結合生產實際,設計第一次拉深系數m1=0.52。由拉深系數計算公式:
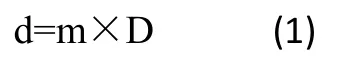
其中,m為拉深系數,d為筒壁直徑(mm),D為毛坯直徑(mm)。計算得首次拉深直徑為d1=107mm。后兩道次拉深系數通過查詢沖壓手冊并結合實際取m2=0.75,m3=0.77。故拉深直徑分別為d2=80mm,d3=61.3mm。凹模圓角半徑的計算公式如公式2所示:

其中,t 為坯料厚度(mm),D 為毛坯直徑(mm),d為第一次拉深后筒壁直徑(mm)。計算出第1次拉深中凹模圓角半徑r1為14mm。由此可確定出后續拉深的凹模圓角半徑為:r2=10mm,r3=7mm。由于內筒的成形屬于變薄拉深,在經過三道次的拉深成形之后需經過冷鐓工步對內筒筒壁增厚,故前三道次的拉深高度需大于零件內筒的圖紙尺寸,結合實際生產經驗前三道次拉深高度為h=24mm。
有限元模型建立
利用Pro/Engineer建立工件和各道次模具的三維模型,基于Deform-3D軟件對多道次成形過程進行模擬分析,模擬采用“SI”公制單位,實際生產中材料為DD13,模擬選擇材料庫中與之相近的AISI-1008,坯料設置為塑性體,模具為剛性體,網格數量劃分為150000個,并運用局部網格細化技術對坯料中間部分進行網格細化分。根據生產實際將摩擦因數設置為0.12,沖壓速度為10mm/s,溫度為20℃。圖3所示為第一道次模具結構。
模擬結果分析
第一道次至第三道次有限元模擬的等效應變分布如圖4所示。由圖4(a)可見應變值較大處出現在內筒上下圓角處,即內筒上下圓角處變形程度較大。由于第二道次和第三道次的拉深高度不再變化,只在筒徑上發生變化,故內筒的上側圓角處應力較為集中,如圖4(b)和圖4(c)所示。第三道次筒徑縮小到61.3mm,已近似于零件內筒直徑61mm,此時內筒圓角及筒壁處壁厚發生了減薄。有限元模擬過程中未出現刮料、折疊缺陷,成形質量較好。
第四道次冷鐓成形內筒。由于前三道次的拉深使內筒筒壁及圓角處有所減薄,所以冷鐓內筒的目的是增厚內筒筒壁及內筒上側圓角以保證后續零件的成形質量。冷鐓工藝是一種精密塑性成形技術,具有制品的機械性能好、生產率高和材料利用率高,特別適合于大批量生產等優點。由圖5等效應變分布圖可知,坯料內筒上圓角處應變值較大,因上圓角處圓角半徑較大,在上模下壓時坯料上圓角處與下模發生刮蹭,故出現應力集中的現象。從成形結果上看內筒筒壁及上側圓角處金屬充填飽滿,滿足后續加工要求。鍛壓成形過程中最大載荷出現在該道次,第四道次載荷圖如圖6所示,最大載荷為184噸。